ISO/TS 29001:2010, also known as API Specification Q1, is a quality management system standard specifically designed for organizations in the petroleum, petrochemical, and natural gas industry supply chain. This standard outlines the quality management requirements for product and service supply organizations in this sector. ISO/API Spec Q1 is applicable to organizations of various sizes and […]
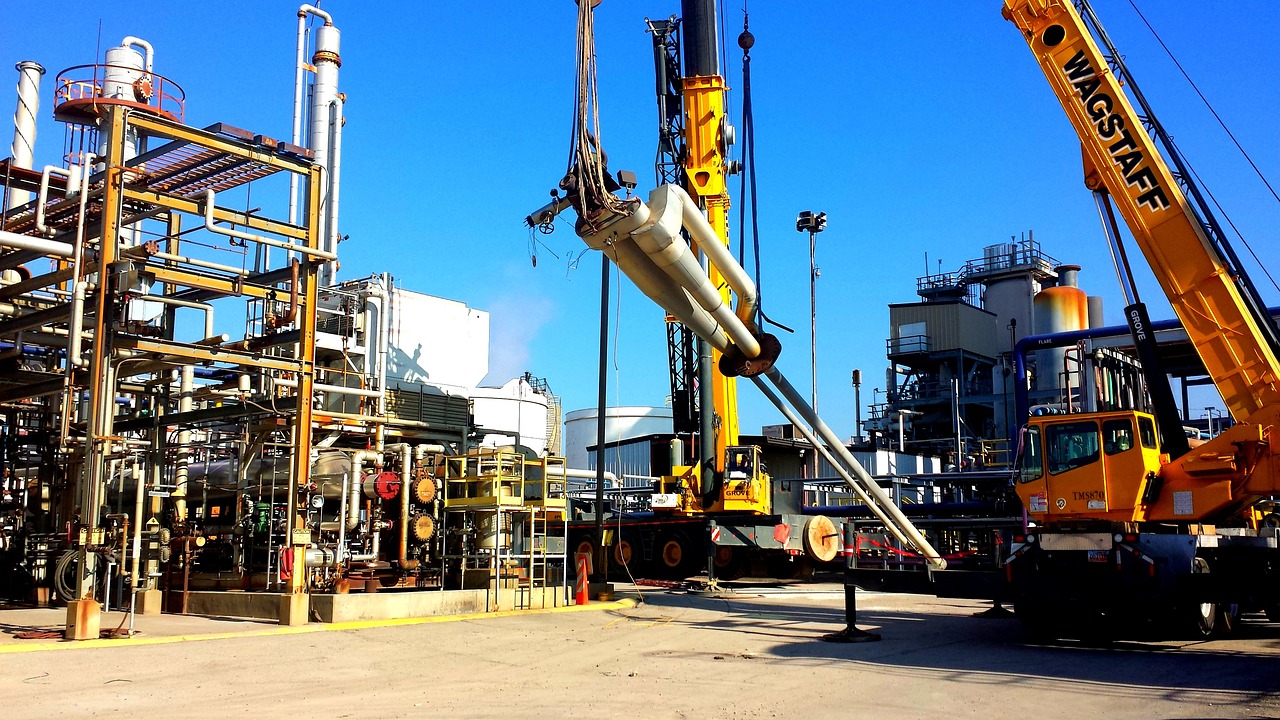